|
Processing centres Optimat BAZ 211 and 222
Description With the "Optimat" series, the Homag Group offers a low-cost alternative to the customized special machine range. All the Optimat machines are equipped with the same leading-edge technology and the same legendary degree of quality and reliability that you have come to expect from Homag products. However, as the Optimat range is series produced, it comes at a substantially lower cost to you. And you also benefit from gratifyingly short delivery and installation periods.
Stationary, modular, reasonably priced Due to the investment volume involved, stationary universal process engineering using CNC technology has usually been reserved in the past to industrial producers. With its Optimat BAZ 41, Homag is now able to offer the cabinet shop and interior fittings trade a particularly reasonably priced, open end solution offering outstanding scope for future upgrading which offers profitable production for even the smallest batch sizes. The machine offers the advantage of being able to edge the workpieces immediately following sizing.
The whole range of sizing, profiling, drilling, grooving and dividing processes as well as edge banding with complete finish processing: The Optimat BAZ41 offers precisely the wide spectrum of possibilities you need to address your every-day production needs. And using every conceivable type of material: Chipboard, MDF, coreboard, solid wood, plastic etc.
The interface The open four-dimensional interface opens up unlimited scope for unit technology: - Power transmission - with a 12 kW asynchronous threephase motor - C axis - rotation of units around their own axis up to 360 degrees - Pneumatic transmission - e. g. for intermittent unit control - Electric/electronic connection for the transmission of control pulses
All units can be exchanged into the working spindle via the interface from a magazine. The 12 kW working spindle is required to fulfil a wide variety of functions, and is equipped with the very best that modern technology has to offer:
- Hybrid bearings (ceramic) = less friction, double the service life, maximum precision - Maximum static and dynamic rigidity, ensuring a high degree of exchange and repeat accuracy - Standardized tool interface HSK F63
Gluing technology Making use of the universal interface, a number of gluing units are available for exchange mounting in the working spindle:
Unique from Homag: Exchange mounting gluing unit (also retrofittable) The "4-side gluing unit" is designed to permit the low-cost, precise edging of shaped components on all sides. The unit is engaged and mounted in the interface of the working spindle by a pick-up system.
If required, the unit can be quickly removed from the pick-up station for simple maintenance and cleaning. The simple, low-cost gluing unit works with pre-coated edging material and is quickly ready for use without any heating-up delay.
360ยบ gluing unit The gluing unit is also taken from the pick-up station as required and exchange mounted in the working spindle. It is designed for fault-free all-round gluing. Both ends of the edging abut so precisely that only a hair-line joint is visible. The gluing head naturally also takes inside radii easily within its stride (up to R = 30 mm). The basic version operates with manual edge guidance. Glue application takes place directly, eliminating the need for the provision of pre-coated edge material.
|
 |
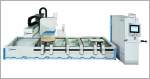
|
|